Shanghai University
Article Information
- Demin ZHAO, Jianlin LIU, C. Q. WU. 2015.
- Stability and local bifurcation of parameter-excited vibration of pipes conveying pulsating fluid under thermal loading
- Appl. Math. Mech. -Engl. Ed., 36(8): 1017-1032
- http://dx.doi.org/10.1007/s10483-015-1960-7
Article History
- Received Oct. 28, 2014;
- in final form May 22, 2015
2. Department of Mechanical and Manufacturing Engineering, University of Manitoba, Winnipeg MB, R3T5V6, Canada
The pipelines for conveying fluids,which have been studied extensively in the past few decades [1, 2] ,are widely used in various industrial sectors,such as the stream generators,nuclear reactors,and chemical and petrochemical industries. Certain nonlinear dynamics behaviors, such as parametric,external,and internal resonances,as discussed in Refs.[3]-[7],can have catastrophic effects on the safety and the functions of these pipelines and the environment. Thus,the proper design of the pipelines and their control to prevent such catastrophic events is extremely important and requires an in-depth understanding of the above mentioned nonlinear dynamic behaviors.
From the viewpoint of nonlinear dynamics,the internal resonance of a pipe can be induced by the natural frequencies of the vibration modes when the ratios of such natural frequencies and the velocity of the fluid reach to certain values. The parameter excited resonance can be induced by the internal turbulence of the flow. Xu and Yang [8, 9] have investigated the mechanism of the internal resonances between the vibration modes of a pipeline induced by the flow velocity. Their studies revealed that (i) the internal resonance occurs when the natural frequency ratio between the second and first vibration modes reaches to 3:1,and (ii) the periodic motion becomes unstable near the critical fluid velocity by jumping or flutter nonlinear dynamics behaviors. Researchers [7, 8, 9, 10] have studied the internal resonance combined with the external resonance for the supercritical velocity regime and obtained the relationship of the amplitudes for the two modes. The jumping,hysteresis,saturation,and other complex dynamics behaviors were also presented and discussed.
The parametric and the internal resonances of pipelines conveying fluids are also accom- panied by many complicated nonlinear dynamics behaviors such as flutter,bifurcation,and chaos [11, 12, 13, 14, 15, 16, 17] . Panda and Kar [4, 5] investigated the stability and the bifurcation of a pipe un- dergoing the combination of parametric and internal resonances. The periodic,quasi-periodic and chaotic responses have all been observed in their system. In addition,the post diver- gence behaviors including supercritical and subcritical pitchfork bifurcations of extensible fluid- conveying pipes supported at both ends were studied by Modarres-Sadeghi and Paidoussis [18] . Jin and Zou [19] investigated the local bifurcation of the pipes with the motion-limiting con- straints and linear spring support,and they proved the existence of the quasi-periodic motion and revealed the route to chaos through the breakups of the quasi-period torus surface. Nikolic and Rajkovic [20] discussed the influence of the gravitational force,curvature,and vertical elastic support on the bifurcation solutions.
Most above-mentioned analyses have been based on the single-,two- or multi-mode approx- imation of the solutions [3, 4, 5, 7, 10, 11, 12, 16, 18] . Two- or higher than two-mode approximations have a higher accuracy of the solution for the pipe internal resonance compared with the single-mode only approximation [11] . However,multi-mode approximations make the analysis complex,te- dious,and unfeasible for the theoretical analysis. Moreover,it has been discussed in Ref.[21] that the single-mode approximation of the solution is adequate to capture the dynamic features, to determine the acceptable limits of the pipe vibration and the natural frequencies,which is the foundation of the design criteria for the acceptable level of machinery vibration. Results of Ref.[12] have demonstrated that both the single- and two-mode approximations essentially give the similar qualitative behavior for the parametric vibration of the pipe under study. Moreover, single-mode approximations may lead to solutions revealing fundamental properties of the pipe system,which is not feasible using the two-mode or higher-mode solution approximations. Our current concern is the vibration induced by the thermal load of the pipes. In many pipeline applications,such as the stream generator,and chemical and petrochemical industries, the fluid is normally transported heatedly through the pipes,and the velocity of the internal fluid often has a harmonic component [22, 23] . In this process,the effects of the thermal loads on the thermo-elastic relationships of pipe materials and on the nonlinear dynamics behaviors of the pipe have become important and challenging. Although some literatures have focused on the pipe or the container dynamics conveying heated fluids using the cylindrical shell model [23, 24] , to the best of our knowledge,there is still a lack of systematic exploration on the thermal load effects on the stability and the bifurcation of long and thin pipes [25] . Therefore,the objectives of the present work are (i) to analyze the stability and the bifurcation of the pipes conveying fluctuant flow under thermal loads,(ii) to develop a mathematical model governing a simply supported pipe conveying the heated fluid,(iii) to reveal the relationship between the thermal field parameter and the dynamic behaviors of the pipe,and (iv) to give valuable information for the design of the pipeline and the controllers to prevent the structural instability.
The paper is organized as follows. In Section 2,the dynamic equations of the pipe under thermal loads are developed based on the Hamilton principle. The Galerkin method is then applied to discretize the partial differential equations into the ordinary differential equations in Section 3. In Section 4,the stability and the local bifurcation of the lateral parametric reso- nance in both unfolding space and physical state space are analyzed,followed by the numerical simulations in Section 5. Finally,the results and discussions are detailed in the physical state space to gain insights into the pipeline dynamics.
2 Equation of motionIn this paper,we consider a vertical pipe with a length L,an internal cross-section area A, a mass per unit length m,and a flexural rigidity EI. The mass per unit length of a conveying fluid M has an axial velocity U varying with time,referring to a Cartesian coordinate system (OXY ). The pipe is assumed as an Euler-Bernoulli beam initially aligned with the X axis, which is in the direction of gravity. The pipe is assumed to oscillate in the XY -plane. The displacements of the pipe along the X-axis andY-axis are denoted by u and v,respectively [1] . The strain of the pipe without considering the thermal load influence can be written as follows [1] :
where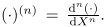
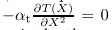


(9) and (10) are the partial differential equations,of which the close-form solutions are rarely found. The Galerkin method is an indispensible method to obtain the approximated solutions. Assume that ū(x,τ) and ¯v(x,τ) can be approximated by the single-mode solution or the two-mode solution below:
or In (11),q1(τ) and q2(τ) represent the longitudinal and lateral vibration amplitudes of the single-mode solution in the X-direction and the Y-direction,respectively. In (12),q11 and q12 are amplitudes of the longitudinal vibration of the two-mode solution,and q21 and q22 are the counterparts of the lateral vibration. Substituting (11) into (9) and (10),multiplying the resultant equations by sin(πx),applying the integration from 0 to 1,and considering the orthogonal property of trigonometric functions,we arrive at a set of reduced second-order ordinary differential equations in the coordinates (q1 ,q2) T as follows: Similar to the single-mode discretization,using (12),we can obtain the reduced ordinary differ- ential equations in the coordinates (q11 ,q12 ,q21 ,q22)T for the two-mode discretization. Due to the lack of space in the paper,the two-mode approximation is compared with the single-mode one to demonstrate that the single-mode approximation is adequate for the lateral parametric resonance analysis.Assume that the pulsating velocity of fluid has the following expression:
where
Since the lateral motion has more effects on the pipe dynamics than that of the longitudinal motion,and (16) and (17) are uncoupled,the lateral motion formulated by (17) is discussed exclusively.
4 Stability and local bifurcation analysis of parametric excited vibrationThe system,shown in (17),has positive stiffness when Δ21 is greater than zero and conversely it can have negative stiffness. When the stiffness Δ21 is close to zero for both positive stiffness and negative stiffness,the parametric excited resonance will occur.
The parameter ω2 is designated as the dimensionless parameter-excited frequency of the
first mode lateral vibration . The time scale is changed to τω2 → τ 2 . Normalizing
the lateral vibration amplitude q2 with an initial value r v as
,we obtain the following
dimensionless quantities:
In (19) and (20),ε is a small parameter which is used as a book keeping device in subsequent
multi-scale analysis. The coefficients in (19) and (20) are shown in Appendix A. Since the
positive stiffness and the negative stiffness introduce different nonlinearities,as shown in (19)
and (20),they have to be analyzed separately. The analysis procedure and the results for the
case of the positive stiffness are discussed in detail,while only the necessary results for the case
of negative stiffness are presented due to the similarity of the two analysis procedures.
4.1 Stability and local bifurcation analysis for positive stiffness case
Introducing the tuning parameter,σ2 ,which describes the difference between Ω2 and 2ω2, we consider the parametric resonance when Ω2 ≈ 2ω2. When ω2 = 1,and Ω2 = 2 + εσ2 ,for (19),the parameter excited resonance will occur according to Ref.[28]. The method of multiple scales is used to search for the approximated solution of (19) in terms of the first-order uniform expansion,and the time scale Tn=εnτ2 (n = 0,1) is introduced. The expansion form of q2 (τ2) is
The first-order approximated solution to (19) can be expressed as The complex variable modulation equation for the amplitude and the phase can be obtained [5] as where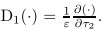

(24) and (25) may have the nontrivial solution,{(a2,θ2 )|a2 ≠ 0,or θ2 ≠ 0},and the trivial solution (0,0). To determine the stability of the nontrivial solution (a2,θ2 ) = (a2* ,θ2*),we assume a2=a2*+ Δa2 and θ2 = θ2* + Δθ2 ,where Δaa2 and Δθ2 are the small perturbations. Substituting the above expression for a2 and θ2 into (24) and (25) yields the following ordinary differential equation for variables (Δa2,Δθ2)T:
where
Setting the right-hand sides of (24) and (25) to be zero and cancelling θ2 ,we arrive at the bifurcation equation,
(29) may be further rewritten as (30) is the codimension-2 universal unfolding bifurcation equation with Z-symmetry. The universal unfolding of (30) is given by where δ1 and δ2 are the unfolding parameters,η is the bifurcation parameter,and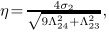

![]() |
Fig. 1 Sketch of transition sets |
![]() |
Fig. 2 Bifurcation diagrams for different unfolding parameter regions |
Some sophisticated dynamics phenomena are also exhibited in Figs.2(a)-2(e),such as jump- ing of the vibration amplitude due to two stable solutions coexisting at certain values of η. Figures 1 and2 provide comprehensive information about the effects of the parameters on the nature of solutions,such as the types of solutions (equilibrium points or limit cycles) and their stability properties. Such information is significant for the design of the pipeline and the controllers to prevent the structural instability. 4.3 Local bifurcation in physical parameter space
The bifurcation analysis in the unfolding parameter space is impossible to give direct infor-mation about the influence of the thermal rate c1 on the dynamic behaviors of the system. In
order to investigate the influence of the thermal rate c1 on the stability of the equilibrium point
and the limit cycle oscillation (LCO),we map the unfolding parameter space into the physical
parameter space. In this work,the assumption of d2 = 0 is made to simplify the calculation
without compromising the accuracy because of the coefficients of the thermal expansion for
the pipe material of the steel,a ≈ O(10 _5 ) and
. In this study,c1 is varied,other
parameters are kept constant,and the following two equations are solved:

![]() |
Fig. 3 Sketch of divided physical parameter space |

In this section,we first demonstrate the accuracy of the single-mode solution. We then present the results of the bifurcation analysis using such a single-mode solution to reveal (i) the relationship between the amplitude of vibration,a2 ,and the tuning parameter,σ2 ,and (ii) the effects of the fluid velocity on the critical thermal rate c1*. In simulations,the physical parameters of the pipe lateral vibration dynamic system are chosen from Ref.[25]. Such parameters are E = 194GPa,I = 5970mm4,m = 1.2706kg/m, M = 0.1602kg/m,A = 160mm2,a = 1.1 × 10-5/◦C,and h = -140E. Throughout the paper unless specifically stated,other parameters used in the simulation are r v = 0.002,e = 0.02, U1 : U0 = 1 : 10,Γ0=0,P=0,U0 = 10m/s,L = 5m,and σ2 = 0. The simulation program was written in MATLAB using the 4th-order Runge-Kutta method. The time step was set as 2 × 10-5. The MAPLE was used to plot the frequency resonance responses and to calculate the theoretical critical thermal rate c1*. 5.1 Comparison between single-mode solution and two-mode solution
In this subsection,we compare the Galerkin single-mode approximated solutions to the two- mode one based on (11) and (12) in Section 3. Two cases are chosen to be presented here, which include c1 =-2.5 and c1 = 1.275. The single-mode and two-mode discretizations of longitudinal and lateral vibrations for the above two cases are plotted in Fig. 4 and Fig. 5, respectively. As shown in Fig. 4(a) and Fig. 5(a),the amplitudes of the longitudinal vibration, q1 and q11 ,are very close,while q12 has a magnitude of 20 percent of the ones of q1 and q11 . As compared with the lateral vibration,the magnitudes of the longitudinal vibration are extremely low (10-7 versus 10-4). Thus,the longitudinal vibration can be neglected. However,consid- ering the lateral vibration,as shown in Fig. 4(b) and Fig. 5(b),the single-mode solution,q2 ,is reasonable close to the two-mode solution,q21 ,while q22 is approximately zero.
![]() |
Fig. 4 Amplitudes of longitudinal and lateral vibrations of single-mode and two-mode discretizations for thermal rate c1=-2.5 |
![]() |
Fig. 5 Amplitudes of longitudinal and lateral vibrations of single-mode and two-mode discretizations for thermal rate c1=1.275 |
More simulations comparing the single-mode solutions with the two-mode solutions have also been carried out with other values of the parameter c1 . Similar results have been obtained in that the single-mode solutions approximate the two-mode solutions reasonably well when c1 < c1 _ 2. Therefore,the first-mode approximated solution of (14) is sufficient to investigate the pipe lateral vibration when c1 < c1_2
5.2 Relationship between tuning parameter and amplitude of vibrationIn this subsection,firstly,we demonstrate the validity of the stability and bifurcation anal- ysis. Secondly,we derive the relationship between the resonance amplitude a2 and the tuning parameter σ2 ,which is important for the design of the pipeline systems. Figures 6 and 8 show the results of the stability and bifurcation analyses as discussed in Section 4 using MAPLE. Figures 7 and 9 are the simulated lateral vibration responses with different thermal rates using MATLAB.
![]() |
Fig. 6 Frequency response curve for c1=1.275 (positive stiffness case) |
![]() |
Fig. 7 Time history of q2 for c1= 1.275 and σ2= 0 |
![]() |
Fig. 8 Frequency response curve for c1= 1.31 (negative stiffness case) |
![]() |
Fig. 9 Time history of q2 for c1= 1.31 and σ2 = 0 |
When the thermal rate c1 =1.275,the system has positive stiffness. In the unfolding param- eter space,the system parameters,δ1 and δ2 ,are located in the region (j),as shown in Fig. 1, and in the physical parameter space,c1 is located in {c1* < c1 < c1 _ 2 } as shown in Fig. 3. In these regions,the system has periodic solutions. Based on (29)-(34),the frequency response is shown in Fig. 6. Selecting σ2 = 0 as an example,the time history of q2 is shown in Fig. 8 with the amplitude of q2 as 1.06 × 10-4. Comparing Fig. 6 with Fig. 7,the amplitude of theoretical analysis a2 as shown in Fig. 6 is 1.16×10-4,which is consistent with the numerical simulation.
When the thermal rate c1 = 1.31,the system has negative stiffness. In the unfolding param-eter space,the system parameters are located in the region (j) and in the physical parameter space,c1 is located in {c1 _ 3 < c1 < c1 _ 4 }. The frequency response and the time history of the lateral vibration are shown in Fig. 8 and Fig. 9,respectively. In Fig. 9,the amplitude of q2 is 3.86×10-4 when σ2 = 0. Comparing Fig. 8 with Fig. 9,the amplitude of the theoretical analysis of q2 as shown in Fig. 8 is 3.92 × 10-4,which is consistent with the numerical simulation. The consistence among the results from the stability and bifurcation analysis and the simulations for the above two cases of different thermal rates confirm the validity of the bifurcation analysis. We next discuss the relationship between the tuning parameter and the lateral vibration. For the case of the positive stiffness,Fig. 6 depicts that the system will converge to a unique equilibrium point under the condition of the tuning parameter,σ2 ? _0.19. When _0.19 < σ2 < 0.19,the system has one stable periodic solution. When σ2 ? 0.19,the system coexists three solutions including one stable equilibrium point,one stable periodic solution,and one unstable limit cycle. This means that the system will converge to different solutions for different initial values. This result indicates that the jumping phenomenon exists when σ2 ? 0.19. For the case of the negative stiffness,Fig. 8 shows that the system coexists three solutions,one stable limit cycle,one unstable limit cycle,and one stable equilibrium point. As σ2 changes from negative to positive,the amplitude of the periodic solution increases gradually.
5.3 Effects of fluid velocity on critical thermal rateThe critical thermal rate c1* can provide important conditions under which the attractors of the systems change from the stable equilibrium point (0,0) to the limit cycle. Such information is important for the pipeline design and vibration control. We determine c1* using MAPLE through stability and bifurcation analysis by solving (35) as discussed in Section 4. We also determine c1* by solving (14) numerically using the Runge-Kutta scheme in MATLAB. The numerical process is briefly described as follows: Firstly,the fluid velocity is fixed,and certain thermal rate of c1 is selected. We then solve (14) and determine the system attractors as an equilibrium point or a limit cycle by observing the solution trajectories. If the attractor is an equilibrium point,c1 will be increased,and the simulation will be conducted again. If the attractor is a limit cycle,c1 will be decreased for simulations. Such a process is iterated to certain values of c1 ,such that the attractor changes from an equilibrium point to a limit cycle, or vice versa. This specific value,c1 ,is the critical thermal rate,c1*,corresponding to this specific fluid velocity. Figure 10 shows the critical thermal rate for different fluid velocities and pipe lengths. From Fig. 10,we observe that the critical thermal rate c1* decreases as the fluid velocity increases regardless of the pipe lengths. Moveover,the critical thermal parameter c1* decreases as the length of the pipe increases regardless of the fluid velocity. Figure 10 shows that,although the critical thermal rate c1* determined from the theoretical analysis is slightly lower than the one from the numerical analysis,they are overall very close with the maximum error within 21.3 percent. However,the theoretical analysis has the advantages in that it only requires solving the parabolic algebraic equation symbolically once,while the numerical analysis requires solving the ordinary differential equation for a large amount of times,which is time consuming.
![]() |
Fig. 10 Critical thermal rate via fluid velocity for different pipe lengths |
In this subsection,the findings in the physical parameter space discussed in Subsection 4.3 are demonstrated through simulations. Such findings include (1) when the parameter c1 satisfies {c1 |c1≤ c1 _ 1 } or {c1 |c1 ≥c1 _ 4 },the system converges to the unique stable equilibrium point,and (2) when the parameter c1 satisfies {c1 |c1 _ 1 < c1 < c1 _ 4 },the system converges to a stable limit cycle at certain σ2 . We choose L = 5m and U0 = 10m/s. In this case,c1* = 1.262 and c1 _ 4 = 1.32 are detected via theoretical analysis in Subsection 4.3. The phase plane trajectories of Eq. (14) via the Runge-Kutta numerical technique are obtained as shown in Figs.11(a)-11(d). On average,iterations are performed 1.585 × 106 time-steps,while the steady state are obtained after 1.0 × 106 time-steps. Figures 11(a)-11(d) are obtained from 1.0 × 106 to 1.585× 106 time-steps. The system converges to the equilibrium point (0,0) as shown in Fig. 11(a) when c1 = 1.25, which is under the condition c1 ≥ c1* as shown in Fig. 3. The system converges to a limit cycle when c1 = 1.275 and c1 = 1.31,which is under the condition,c1* < c1 < c1 _ 4 ,as shown in Figs.11(b) and 11(c). The system converges to the non-zero equilibrium point when c1 =3.0 as shown in Fig. 11(d),which is under the condition c1 ≥ c1 _ 4. The phase plane trajectory results are consistent with those obtained from the theoretical analysis.
![]() |
Fig. 11 Phase plane trajectories for different thermal rates |
Chaos has been detected in this system as shown in Fig. 12. However,when the chaos occur, the velocity of the fluid and the thermal rates are all higher than the critical velocity and thermal rate when the periodical osscilation happens.
![]() |
Fig. 12 Phase plane trajectory of chaos when L = 3m,U 0 = 15m/s,and c1= 3.65 |
In this paper,the stability and bifurcation of the pipes under thermal loads have been systematically investigated under the condition that the ratio of the pulsating frequency of the fluid velocity in the axial direction versus the nature frequency of the pipe is approximate,where the parametric resonance will occur. The main results obtained in the paper are as follows: (i) The single-mode approximation of the solution to the above pipe system under thermal loading is adequate to characterize the lateral vibration. (ii) The relationship of the tuning parameter σ2 and the amplitude of the periodical vibration (or named the frequency response) is obtained. Negative tuning parameters may be beneficial to the stability of the system,because the negative tuning parameter indicates the unique solution such as equilibrium point or the limit cycle,which means that the system will converge to the initial equilibrium state or a periodical vibration on any initial conditions. Higher positive tuning parameters may lead to the jumping phenomena of the system,which means that the system will converge to differential solutions for different initial conditions. (iii) The effects of fluid velocities and pipe lengths on the critical thermal rate have also been investigated. It shows that the critical thermal rate decreases as the fluid velocity increases. The critical thermal rate has the same trend as the pipe length increases. Such findings are important for the pipeline design. (v) Chaos have been detected in this system. However,it only happens when the system is under the condition of a higher fluid velocity and a higher thermal rate. The fluid is often transported heatedly through the pipes in some pipeline industries,and the velocity of the internal fluid has a harmonic component due to the pump and fluid properties. The parametric resonance often occurs,which may have catastrophic effects on the safety and the functions of these pipelines. The investigation of the stability and bifurcation of the pipe system can provide vital information for the design of vibration control for pipe systems conveying heated fluids.
[1] | Semler, C., Li, G. X., and Paidoussis, M. P. The non-linear equations of motion of pipes conveying fluid. Journal of Sound and Vibration, 169(5), 577-599(1994) |
[2] | Paidoussis, M. P. In Fluid-Structure Interactions:Slender Structures and Axial Flow, Academic Press Limited, London (1998) |
[3] | Jin, J. D. and Song, Z. Y. Parametric resonances of supported pipes conveying pulsating fluid. Journal of Fluids and Structures, 20(6), 763-783(2005) |
[4] | Panda, L. N. and Kar, R. C. Nonlinear dynamics of a pipe conveying pulsating fluid with parametric and internal resonances. Nonlinear Dynamics, 49, 9-30(2007) |
[5] | Panda, L. N. and Kar, R. C. Nonlinear dynamics of a pipe conveying pulsating fluid with combination principle parametric and internal resonances. Journal of Sound and Vibration, 309, 375-406(2008) |
[6] | Liang, F. and Wen, B. Forced vibrations with internal resonance of a pipe conveying fluid under external periodic excitation. Acta Mechanica Solids Sinica, 24, 477-483(2011) |
[7] | Zhang, Y. L. and Chen, L. Q. External and internal resonances of the pipe conveying fluid in the supercritical regime. Journal of Sound and Vibration, 332, 2318-2337(2013) |
[8] | Xu, J. and Yang, Q. B. Nonlinear dynamics of a pipe conveying pulsating fluid with combination principle parametric and internal resonances (I). Applied Mathematics and Mechanics (English Edition), 27(7), 943-951(2006) DOI 10.1007/s 10483-006-0710-z |
[9] | Xu, J. and Yang, Q. B. Nonlinear dynamics of a pipe conveying pulsating fluid with combination principle parametric and internal resonances (Ⅱ) (in Chinese). Journal of Sound and Vibration, 27(7), 825-832(2006) |
[10] | Zhang, Y. L. and Chen, L. Q. Internal resonances of the pipe conveying fluid in the supercritical regime. Nonlinear Dynamics, 67, 1505-1514(2012) |
[11] | Paidoussis, M. P. and Semler, C. Nonlinear and chaostic oscillations of a constrained cantilevered pipe conveying fluid a full nonlinear analysis. Nonlinear Dynamics, 4, 655-670(1993) |
[12] | Jayaraman, K. and Narayanan, S. Chaostic oscillations in pipes conveying pulsating fluid. Nonlinear Dynamics, 10, 333-357(1996) |
[13] | McDonald, R. J. and Namachchivaya, N. S. Pipes conveying pulsating fluid near a 0:1 resonance:local bifurcations. Journal of Fluids and Structures, 21, 629-664(2005) |
[14] | McDonald, R. J. and Namachchivaya, N. S. Pipes conveying pulsating fluid near a 0:1 resonance:global bifurcation. Journal of Fluids and Structures, 21, 665-687(2005) |
[15] | Xi, H. M., Zhang, W., and Yao, M. H. Periodic and chaotic oscillation of the fluid conveying pipes with pulse fluid (in Chinese). Journal of Dynamics and Control, 6(3), 243-246(2008) |
[16] | Wang, L. A further study on the non-linear dynamics of simply supported pipes conveying pulsating fluid. International Journal of Non-Linear Mechanics, 44, 115-121(2009) |
[17] | Wang, L. and Ni, Q. Hopf bifurcation and chaostic motions of a tubular cantilever subject to cross flow and loose support. Nonlinear Dynamics, 59, 329-338(2010) |
[18] | Modarres-Sadeghi, Y. and Paidoussis, M. P. Nonlinear dynamics of extensible fluid-conveying pipes supported at both ends. Journal of Fluids and Structures, 25, 535-543(2009) |
[19] | Jin, J. D. and Zou, G. S. Bifurcations and chaotic motions in the autonomous system of a restrained pipe conveying fluid. Journal of Sound and Vibration, 260(5), 783-805(2003) |
[20] | Nikolic, M. and Rajkovic, M. Bifurcations in nonlinear models of fluid-conveying pipes supported at both ends. Journal of Fluids and Structures, 22, 173-195(2006) |
[21] | Drozyner, P. Determining the limits of piping vibration. Scientific Problems of Machines Operation and Maintenance, 1(165), 97-103(2011) |
[22] | Semler, C. and Paidoussis, M. P. Nonlinear analysis of parametric resonances of a planar fluidconveying cantilevered pipe. Journal of Fluids and Structures, 10, 787-825(1996) |
[23] | Ganesan, N. and Kadoli, R. A study on the dynamic stability of a cylindrical shell conveying a pulsatile flow of hot fluid. Journal of Sound and Vibration, 274, 953-984(2004) |
[24] | Sheng, G. G. and Wang, X. Dynamics characteristics of fluid-conveying functionally graded cylindrical shell under mechanical and thermal loads. Composite Structures, 93, 162-170(2010) |
[25] | Qian, Q., Wang, L., and Ni, Q. Instability of simply supported pipes conveying fluid under thermal loads. Mechanics Research Communication, 36, 413-417(2009) |
[26] | Takeuti, Y. Thermal Stress (in Chinese), Science Publishing Press, Beijing (1977) |
[27] | Jekot, T. Nonlinear problems of thermal postbuckling of a beam. Journal of Thermal Stresses, 19, 356-367(1996) |
[28] | Nayfeh, A. H. The Method of Normal Forms, Wiley, Singapore (2011) |
[29] | Golubisky, M. and Schaeffer, D. G. Singularities and Groups in Biurcation Theory, Springer-Verlag, New York (1984) |